graphite electodes
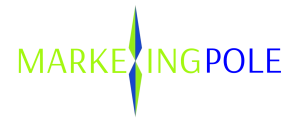
INTRODUCTION
Graphite electrodes are large cylindrical structures serve to transfer the electrical energy from the power supply to the steel melt in the Electric Arc Furnaces (EAF) bath , it is a conductor which releases electric energy in the form of arc in the furnace to heat and melt the charge.
Affected by environmental protection and high production flexibility, the steel-making process is changing from blast furnace and ladle furnace to electric arc furnace (EAF).
They are typically made using premium petroleum needle coke, coal tar pitch, which is used as a binder ,and some additives. Needle coke is a key raw material for the production of graphite electrodes. It is a calcined petroleum coke (CPC) which accounts for about 70% of the input cost of graphite electrode production
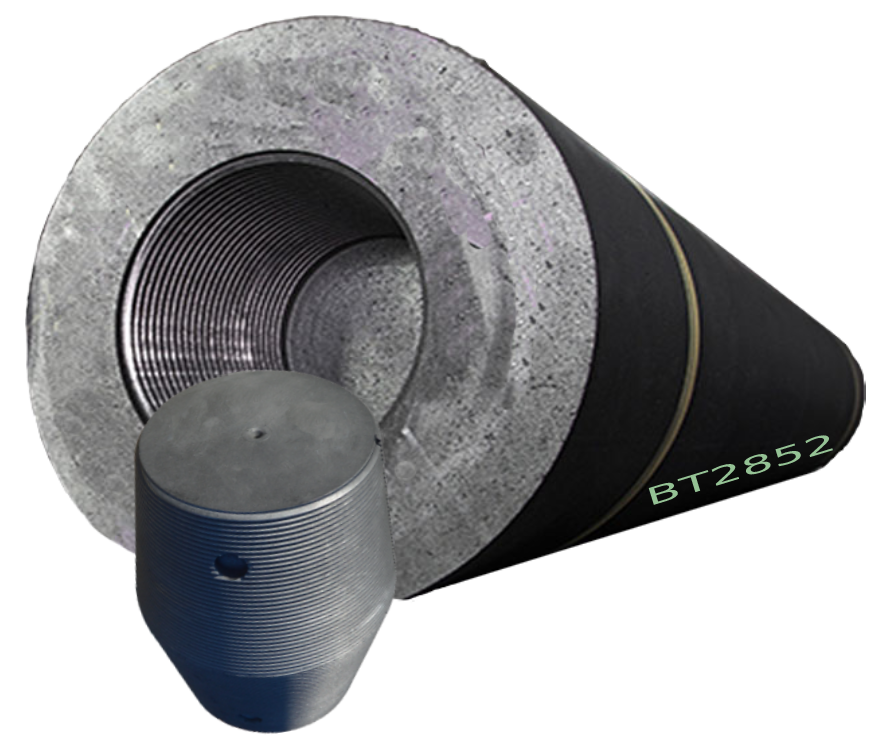
GRAPHITE ELECTRODES PRODUCTION PROCESS
- Raw materials (100% imported needle coke, coal tar pitch).
a) Crushing.
b) Calcining (Calcination).
c) Pulverizing, Weighting, Screening and Dosing (Classify the screened coke according to gain size and store them in individual silos).
d) Mixing (Knead the mixed coke and binder pitch into kneader). - Forming (The kneaded material is formed into green electrode by extrusion press through various press nozzles and by the extrusion press and cut into specified lengths).
a) Water-cooling - Baking (1200 °С, 40-60 days)
- Impregnation
- Re-baking
- Graphitizing – 10 days @ 2800 3000 °С.
- Machining
- Inspection
- Packing
- Shipping
The size of the electrodes varies widely, but can be up to 800mm in diameter and 3000 mm in length. Due to their high level of electrical conductivity and capability of withstanding the extremely high temperatures of up to 1600 degree Celsius, graphite electrodes are a vital input in Electric Arc Furnaces (EAF), ladle refinement of steel and the production of ferroalloys.
Electrodes are classified as
- RP (Regular Power) : mainly used for regular power electric arc furnaces to smelt scrap steel, silicon and yellow phosphorus.
- HP (High Power) : for foundry operation and ladle furnaces and occasionally for electric arc furnaces with the current density range of 18–25 A/cm2
- UHP (Ultra High Power) : for electric arc furnaces , ladle furnace operations with heavy current loads with the current density greater than 25 A/cm2
- SHP (Super High Power) : widely used in super high Electric Arc Furnaces for steel mills .
direct current furnaces (DC furnaces ), which require 1 column of graphite electrodes needs high current density. The diameter of these electrodes is getting bigger that can be about 550 mm -800 mm.
Alternating current furnaces ( AC) that require 3 columns of graphite electrodes mostly use 400mm-700 mm electrodes, and for LF Furnaces (refining furnaces) needs 250mm – 450mm diameter electrodes .Electrode oxidation, sublimation, dissolution, spalling and breaking are all related to the cost of EAF steelmaking. Proper graphite electrode selection, use and maintenance can effectively reduce electrode consumption.
Performance Parameters:
- Specific Electrical Resistance (SER or ER), low specific resistance of graphite electrodes allows maximum current carrying capability without overheating of the electrode column.
- Bulk or apparent density, a higher bulk density will generally be reflected in improved mechanical properties.
- Flexural strength, higher flexural strength in electrodes will generally result in lower electrode breakage frequency.
- Tensile strength, higher tensile strength in nipples will generally results in lower nipple breakage frequency.
- Coefficient of Thermal Expansion (CTE), lower CTE will generally give better resistance to thermal shock. Also, CTE compatibility between the graphite electrode and connecting nipple is important for satisfactory performance of the electrode joint.
if you have any question about product detail please
MARKETING POLE GROUP
Central Office TEL: 0098 5138407354
Email : info@marketingpole.com